I recently returned from MD&M West 2023, and I thought I would share some of my highlights from the trade show expo. MD&M stands for “Medical Design & Manufacturing”. It’s one of the largest gatherings in the industry, filling the 1.6 million square foot Anaheim Convention Center every year. It’s actually several trade shows in one, spanning medical device design services, manufacturing, automation, plastics, and packaging.
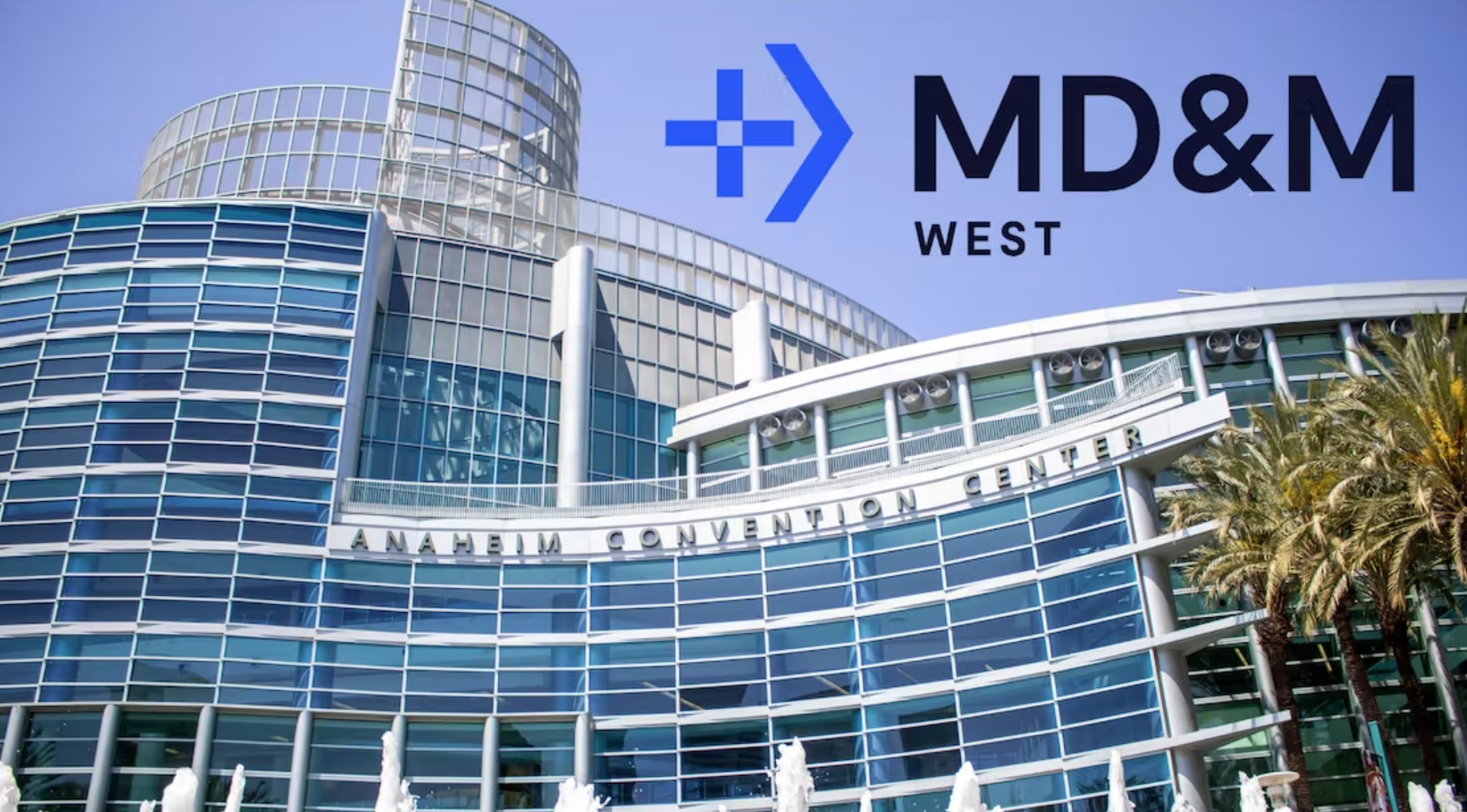
According to my Fitbit, I clocked over 20,000 steps on Tuesday. This is one of my favorite trade shows, and I always come away fired up with new ideas. Please note: I’ve received no compensation from any of the vendors listed here
Lumafield
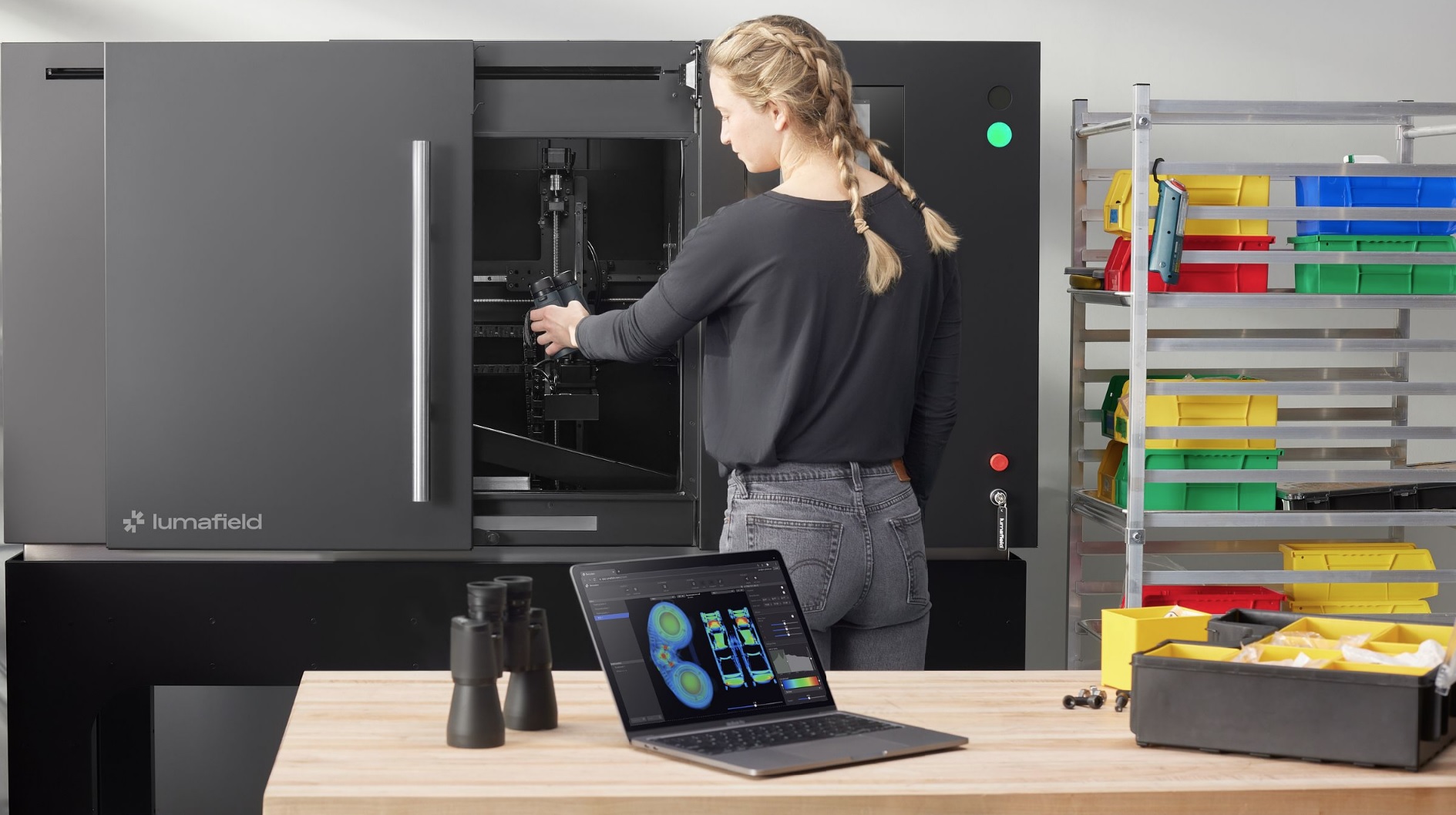
Industrial CT is an invaluable tool for understanding as-built tolerances and defects in your product assembly. Just like in medical imaging, x-ray computed tomography can be used to “look inside” your product with remarkable resolution. By overlaying a CAD model with a segmented CT scan, you can see where your parts are deviating from their design parameters. Until now, Industrial CT was generally limited to metrology labs–you send them parts and, a few weeks later, they send you back a thumb drive full of TIF files. The software to make sense of these TIF files is expensive and difficult to use, and even the best modern laptop strains under all that data.
Enter Lumafield. They describe themselves as a “hardware as a service” company. For $4,500/mo, you can have your very own CT scanner and put whatever you want in there, whenever you want. The data gets uploaded directly to the cloud, where their backend software handles rendering, segmentation, and metrology. This reduces the time it takes to access and make sense of this data from weeks to minutes. As a cloud platform, Lumafield makes collaboration much easier, ensuring that everyone is “seeing” the same thing.
UpNano
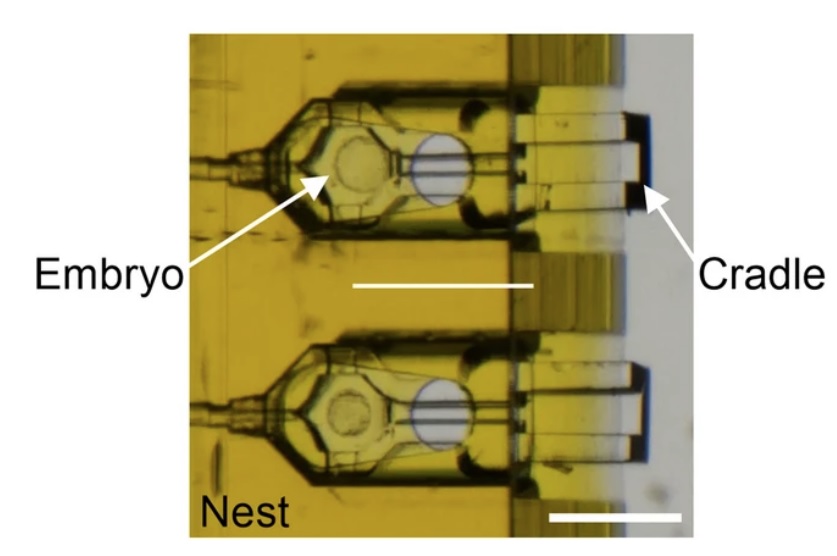
Vention
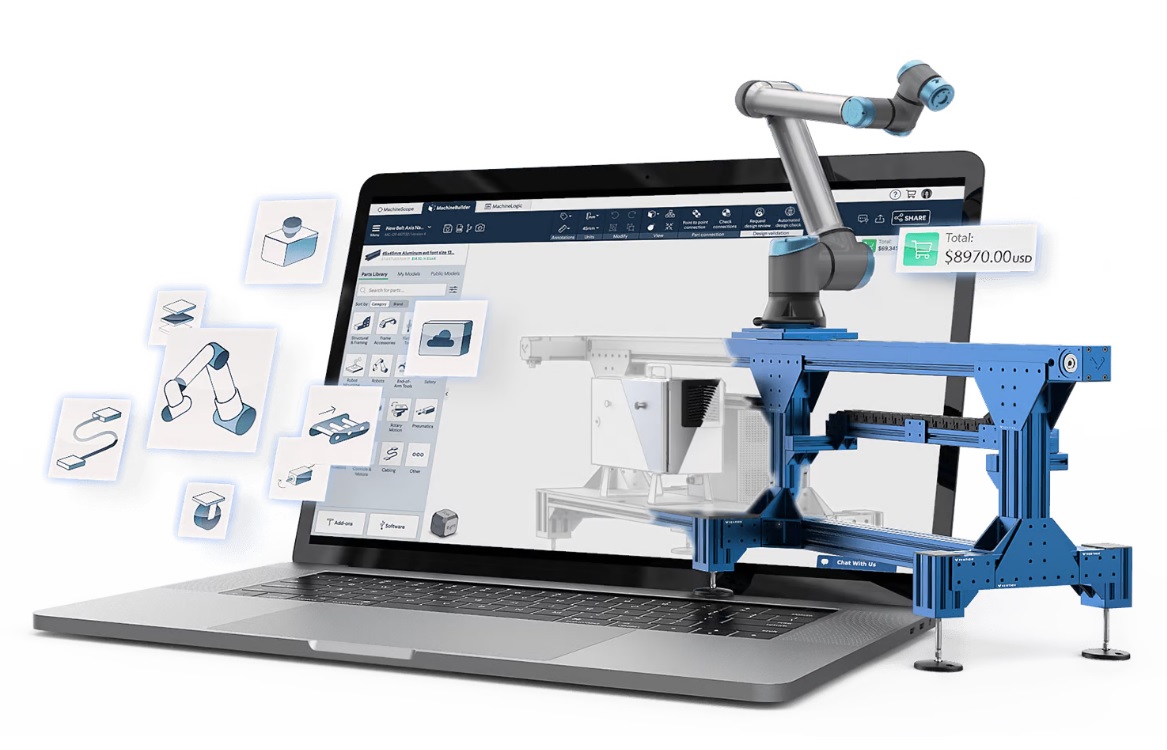
Vention brings this kind of convenience to manufacturing automation. They provide a cloud-based design platform and marketplace for quickly configuring robots, conveyors, and other automation equipment in a 3D virtual environment. They also provide a no-code programming language for simulating and deploying industrial automation sequences and designing custom HMIs. This means that you can develop and test your automation virtually, before ever ordering equipment. Their control appliance is cloud-connected out of the box, meaning once your work cell is deployed, you can monitor it in real-time remotely.
What appeals to me about this platform is that it makes automation process development more accessible, particularly at the early stages of development. Product development typically involves many separate teams: R&D, DFX, NPI/process development, manufacturing, and (often lastly) automation. Limited cross-functional visibility across these teams often leads to cost overruns and delays. By the time automation is being discussed, the product may already be on the market, and design changes may not be feasible. I always advise clients to think of the product design and automation together, and tools like Vention make that much easier.
No doubt, this is only the beginning. I look forward to seeing how these platforms develop, hopefully integrating vision and other kinds of sensor feedback into the simulation environment. I think we’ll also start to see some powerful AI assistance coming to automation design in the coming years.
Mecademic
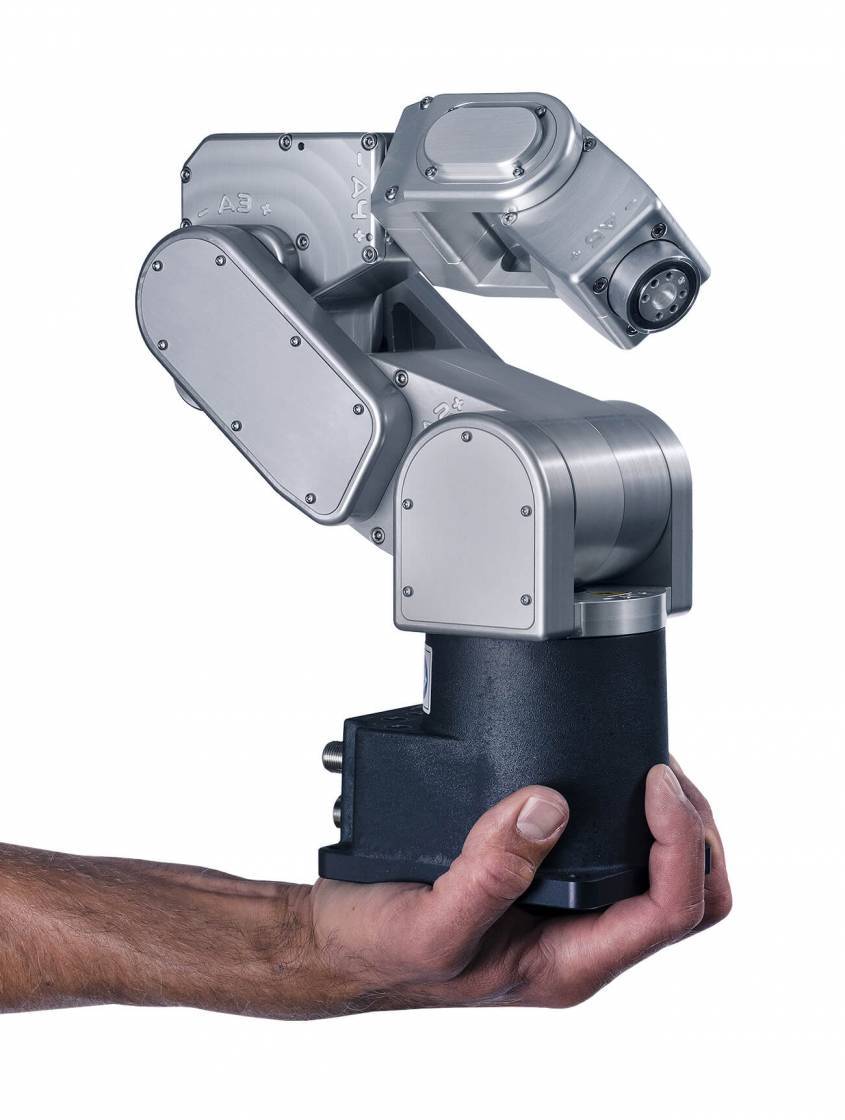
First, there is a growing list of alternatives to the traditional PLCs that have dominated automation control for decades. Many automation components now include their own real-time embedded controllers, eliminating the need for a master cabinet full of 24V relays and pneumatic valves. Instead, systems are coordinated over a TCP/IP network, and the master “conductor” of this automation orchestra can just be a humble PC.
Second, the industry is moving toward programmable, general purpose robotic arms, end effectors, and vision systems. Traditional automation approaches generally involve a series of unit operations, each one highly specialized for a specific assembly step, arranged along a conveyor or rotary dial sequencer. This optimizes for speed, but it is expensive to develop and tends to be difficult to update for future product designs. Robotics, on the other hand, represent a durable capital equipment investment that can be easily reprogrammed and repurposed as products evolve.
Industrial robotic arms are becoming really affordable, and their specs are impressive. One vendor that caught my eye was Mecademic. Their Meca500 is the smallest, most-precise six-axis industrial robot arm in the industry. It boasts 0.005 mm positional accuracy, and it lists at $17,490. This is an ideal platform for assembling small devices and automating tedious lab workflows. It includes an embedded real-time controller that can be programmed with any programming language, eliminating the need for a dedicated PLC.
Planar Motor
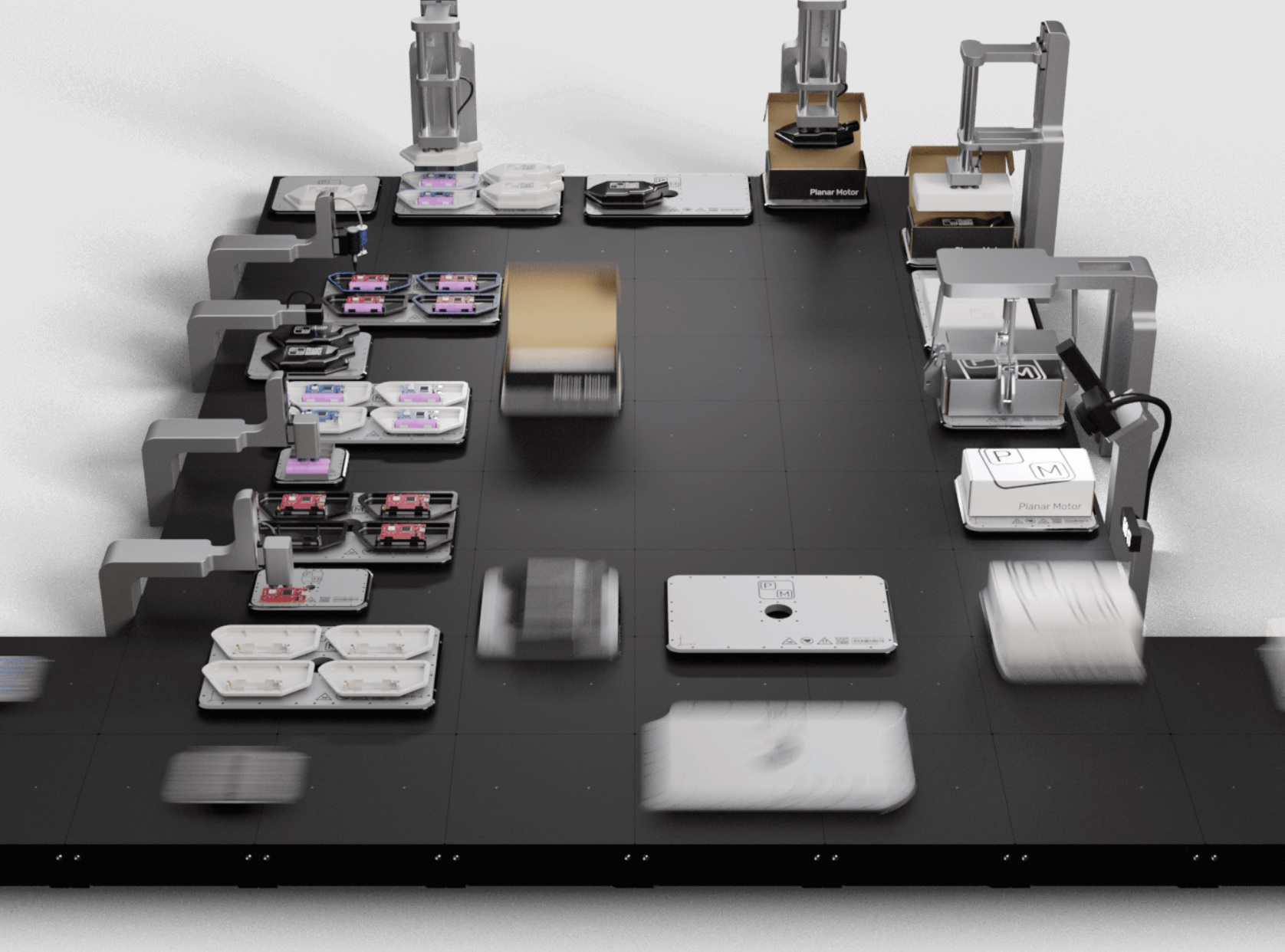
TE Connectivity
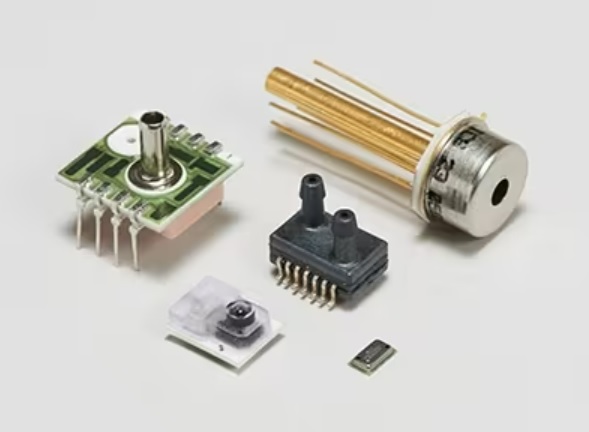
Clippard
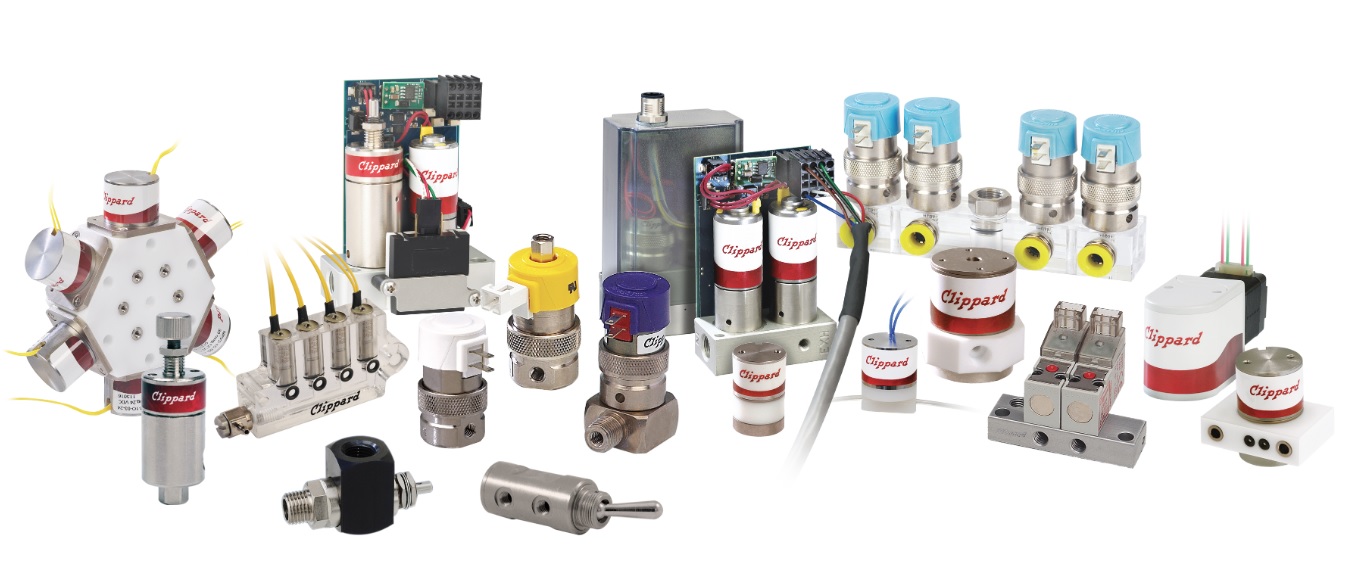
Planet Innovation
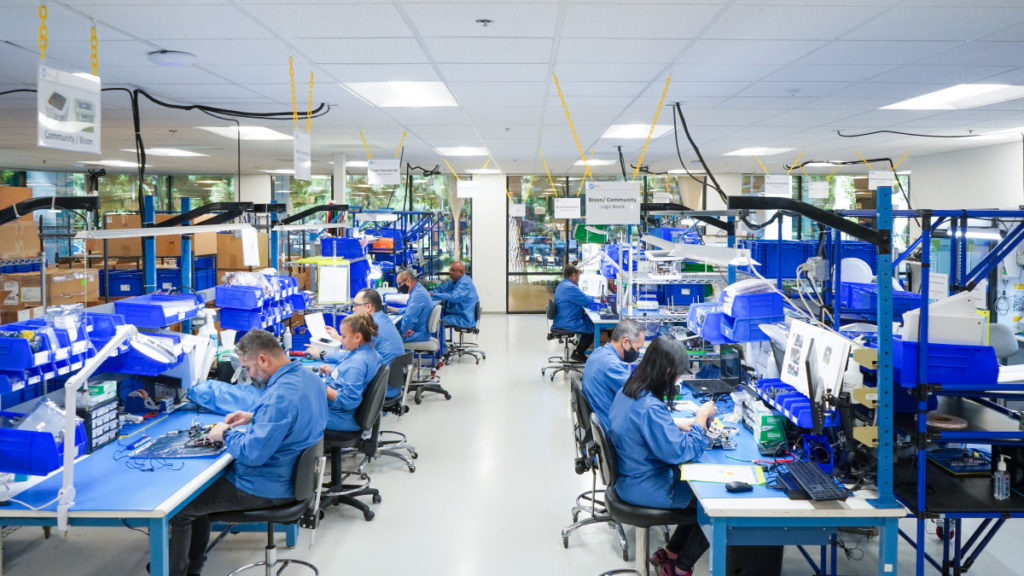
Did I miss something? Shoot me a line and let me know what stood out for you.